What is the minimum maintenance effort that must be performed to keep the goods at a maximum level of operation and to avoid unexpected damage? The answer to this question can be given with the help of predictive maintenance.
Predictive maintenance (PdM) is a type of condition-based maintenance that monitors the condition of assets using sensor devices. These sensor devices provide real-time data that is used to predict when the property will need maintenance and to prevent equipment damage.
According to a report published by Market Research Future, the predictive maintenance market will grow by 25.5%, reaching over 23 million in 2025.
In general, predictive maintenance is used in areas such as the production of goods, health, automotive, transportation, but there is no limitation, any company that uses equipment can benefit from the advantages offered by it.
The purpose of predictive maintenance is to predict when equipment failures may occur, depending on a number of factors, followed by the prevention of such failures through proper and regular maintenance. Having these operations scheduled eliminates both excessive maintenance (unnecessary cost) and unexpected equipment failure. It also increases the life of an equipment when it is maintained before malfunctions occur.
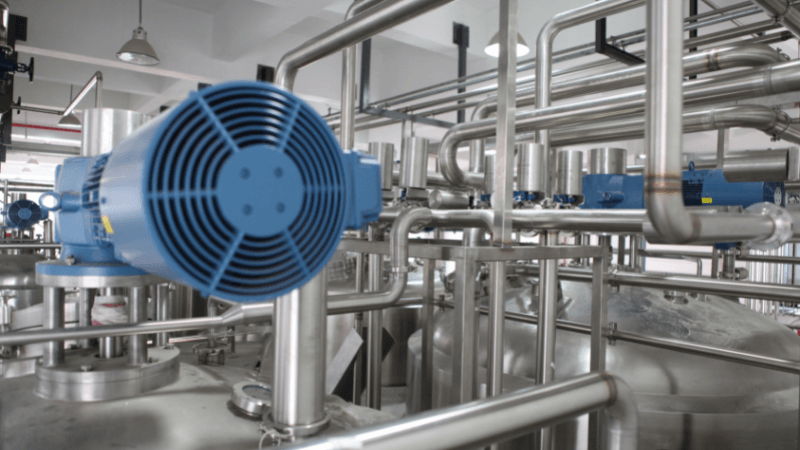
Types of predictive maintenance
There are several types of predictive maintenance: vibration analysis, sonic acoustic analysis, ultrasonic acoustic analysis and infrared analysis.
- Vibration analysis is the type most often used for maintenance by companies that use equipment with a high degree of vibration. It monitors the levels and patterns of vibration signals within a component, machine, or structure to detect abnormal vibration and to assess the general condition of the equipment;
- Sonic acoustic analysis is used for equipment with both low and high degree of rotation. This is the measurement of sound waves caused by the contacts of the components inside the equipment. Devices that detect the frequency of sound use input transducers. Input transducers convert sound into audio signals, which are then interpreted;
- Ultrasonic acoustic analysis identifies friction sounds in a range of ultrasound and is used for mechanical and electrical equipment. This type of predictive maintenance is excellent for anticipating imminent failures. Unlike sonic acoustic analysis (this is limited to the line of proactive and predictive maintenance), ultrasonic acoustic analysis is used exclusively for predictive maintenance efforts. It is claimed that this type of analysis predicts imminent defects better than vibration or oil analysis;
- Infrared analysis does not depend on the rotational speed of a material or the sound volume. Therefore, it is suitable for many types of equipment. When temperature is a good indicator of potential problems, infrared analysis is the most cost-effective tool for predictive maintenance. It is often used to identify problems related to cooling, airflow and even engine stress.
Predictive maintenance components
There are three main components that allow PdM to track the condition of assets and issue an alert for future failures:
- Equipment status monitoring sensors, which transmit real-time performance data and machine health data (e.g. temperature, pressure, noise, etc.);
- IoT (Internet of Things) technology that allows communication between machines, software solutions and cloud technology, which facilitates the collection and analysis of large amounts of data;
- Predictive data models that are fed with all processed data. These predictive models identify trends to detect when a piece of equipment needs service, repair, or replacement. The formulas are based on predetermined algorithms that compare the current behavior of equipment with its expected behavior. Deviations are indicators of gradual damage, which means that action can be taken to avoid equipment failure.
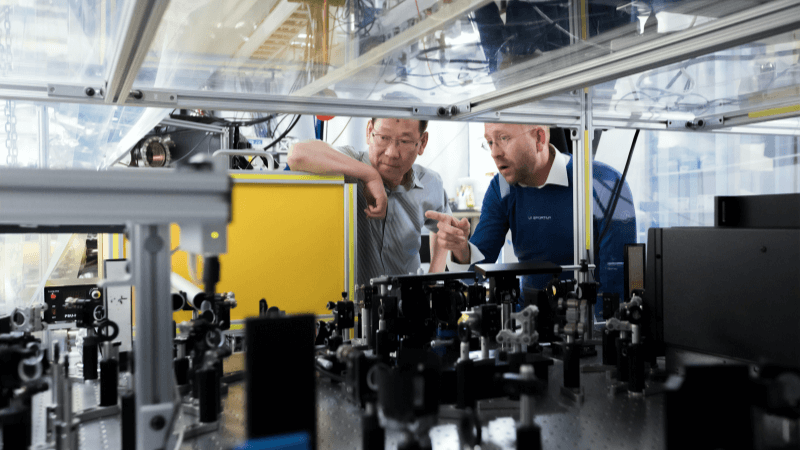
How to implement predictive maintenance
Before starting the implementation process, it is necessary to prioritize the most important resources to be tracked. Here’s how to implement a predictive maintenance program:
1. Identify critical assets: the first step is to identify critical assets and systems that should be included in the program. Prioritize assets with the highest repair and replacement costs.
2. Establish the equipment database and install IoT devices. This information is extremely important for the success of this process. Why? Because it provides useful insights into the car’s behavior. Establish the CMMS database, departmental records and paper files.
What is CMMS?
CMMS (computerized maintenance management system) is a computerized maintenance management system, which has a database with information about a company’s maintenance operations (equipment, materials and other resources).
3. Set Failure Modes. Performs an analysis of critical assets and establishes Failure Modes. Connect IoT devices to a CMMS or remote dashboard for data collection and analysis.
What is Failure Mode?
Failure mode (or “failure mode”) is the ways in which something could fail. Failures are represented by faults and errors, and they can be actual or potential.
4. You have to make predictions of failure. Design a model that addresses failure predictions. This allows you to monitor operating conditions, predict and understand the patterns that are forming, and create alerts on a fully automated system.
5. Implement the system on pilot equipment. Before making a massive launch, perform a pilot test for a selected group of equipment. This allows you to identify all the parts of the system that need to be improved.
What else do you need to consider when you want to create a predictive maintenance program
- make sure that there are people in your team who are familiar with the technical details involved;
- to define from the beginning the available goals and resources;
- to select a method of obtaining data;
- to select the technology, tools and partners with which it interacts on this project;
- to monitor the project performance.
Depending on the size and complexity of the company, it may take some time to see the impact of the new system on operations. However, the successful implementation of a predictive maintenance program will greatly improve business operations, as it will reduce time spent on repairs and unnecessary maintenance, reduce equipment costs, and extend their life.
We have developed a field service management tool, mAIa. This is the best solution for companies that maintain equipment. Learn more about mAIa.